Choosing The Right Cutting Tool Coatings for Optimal Productivity
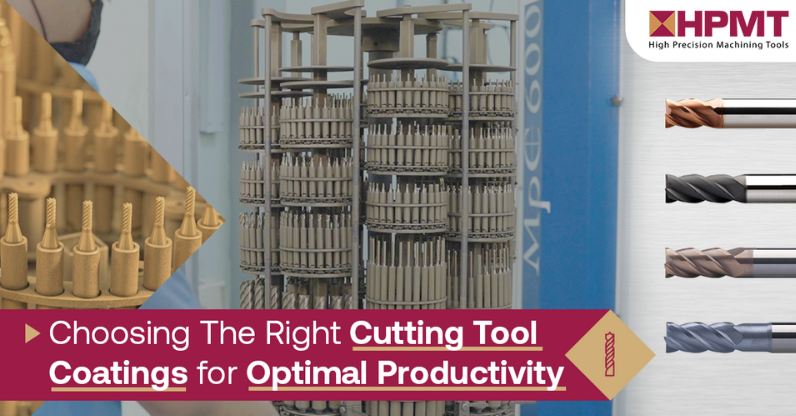
In the world of precision machining, cutting tool coatings play an important role in optimizing efficiency and performance. The right coating can significantly impact tool life, minimize wear, and improve machining efficiency. In this blog, we will delve into the significance of cutting tool coatings, explore the functions of different coating types, and guide you in selecting the right coating for your specific machining needs.
Cutting tool coatings are essential because they provide several advantages that contribute to improved productivity. Manufacturers often opt to apply coatings to maximize the lifespan of these valuable cutting tools and reduce future costs. Coating industrial cutting tools offers a range of benefits:
Wear Resistance: Improve a substrate's ability to resist material loss, ensuring the cutting tool maintains its sharpness and effectiveness for an extended period.
Thermal Barrier: Enable the substrate to withstand higher temperatures without losing its structural integrity.
Lubricity: Enhance the lubricity of the cutting tool, reducing friction during the cutting process.
These coating enhancements ultimately translate into prolonged tool life, improved performance, and reduced costs over time. HPMT offers a variety of advanced coating materials that suit your needs.
Here are some commonly used coatings and their key characteristics:
In the realm of cutting tool coatings, two prominent methods stand out: Chemical Vapor Deposition (CVD) and Physical Vapor Deposition (PVD). While they share the goal of enhancing tool performance, these techniques differ in their approach and outcomes. Here are the distinct characteristics of each method to understand their nuances better.
Chemical Vapor Deposition (CVD)
A long-standing and widely used technique involves heating and exposing the coating material to a vapor state. The vapor reacts on the substrate surface, resulting in the formation of a uniform coating layer. This process boasts excellent adhesion and consistent coating distribution, creating an efficient thermal barrier. However, it requires high temperatures, which may limit its suitability for specific substrates.
Physical Vapor Deposition (PVD)
The machine has gained popularity as a newer coating technique. It operates in a vacuum environment, vaporizing the coating material and subsequently adhering to the substrate. This method offers advantages such as lower temperature requirements, making it more compatible with heat-sensitive substrates. Additionally, PVD enables the coating of sharp edges, expanding its versatility. However, achieving uniform coating distribution can be more challenging with this approach.
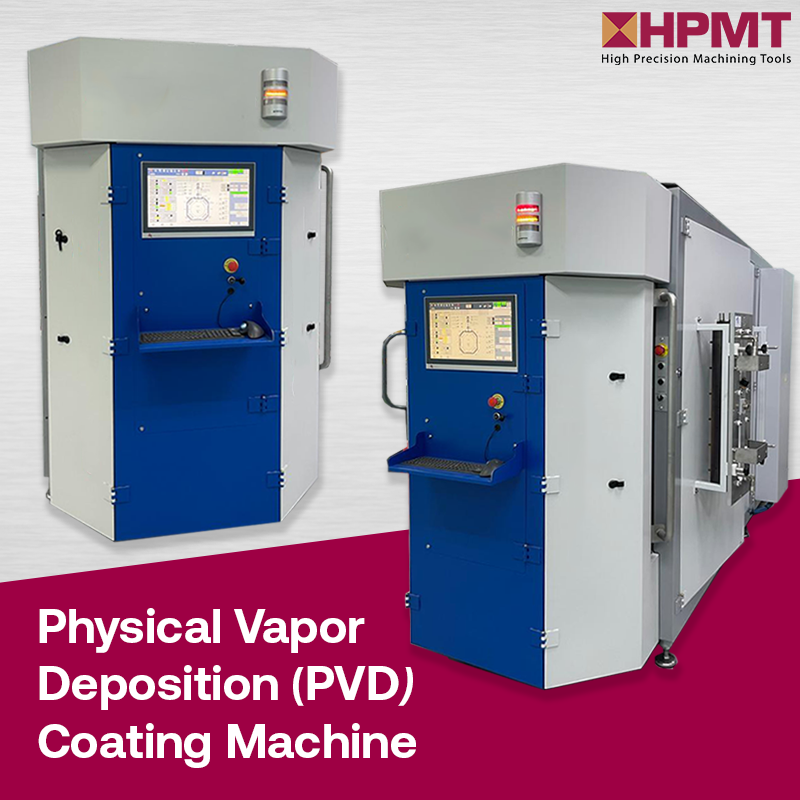
Explore the wide range of coated cutting tools and learn more about how our in-house PVD coating machine can revolutionize your coating processes.
Are you curious about your industrial cutting tools’ ideal coating material and method??
To determine the most suitable coating for your specific application, we highly recommend consulting with our team of industry experts at HPMT.
In conclusion, choosing the right cutting tool coating is vital for improving productivity in precision machining. It directly affects tool lifespan, reduces wear, and enhances machining efficiency. Understanding the importance of cutting tool coatings and exploring their different types empowers you to make informed decisions when selecting the best coating for your specific machining requirements.
HPMT is committed to providing high-quality cutting tools and services to clients worldwide. Contact us today to learn more about our products and services
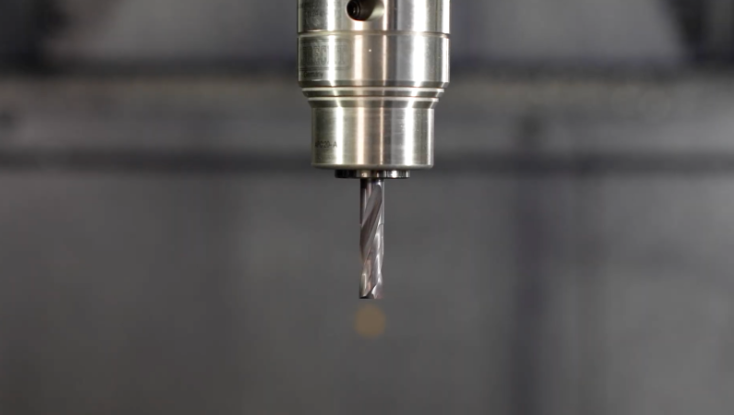
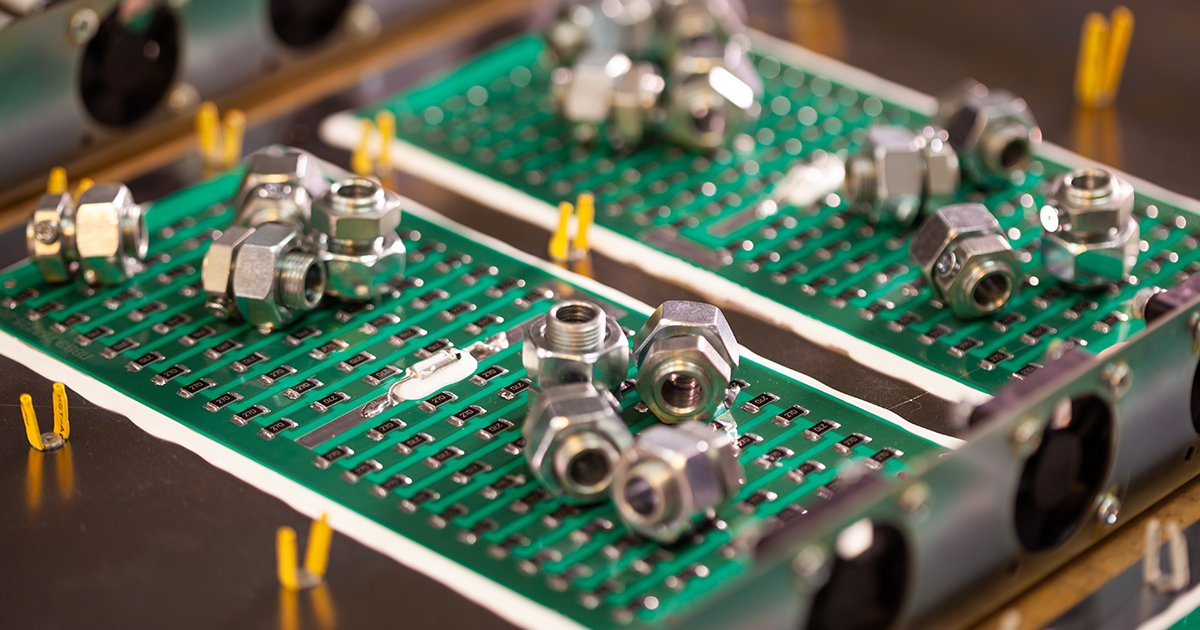
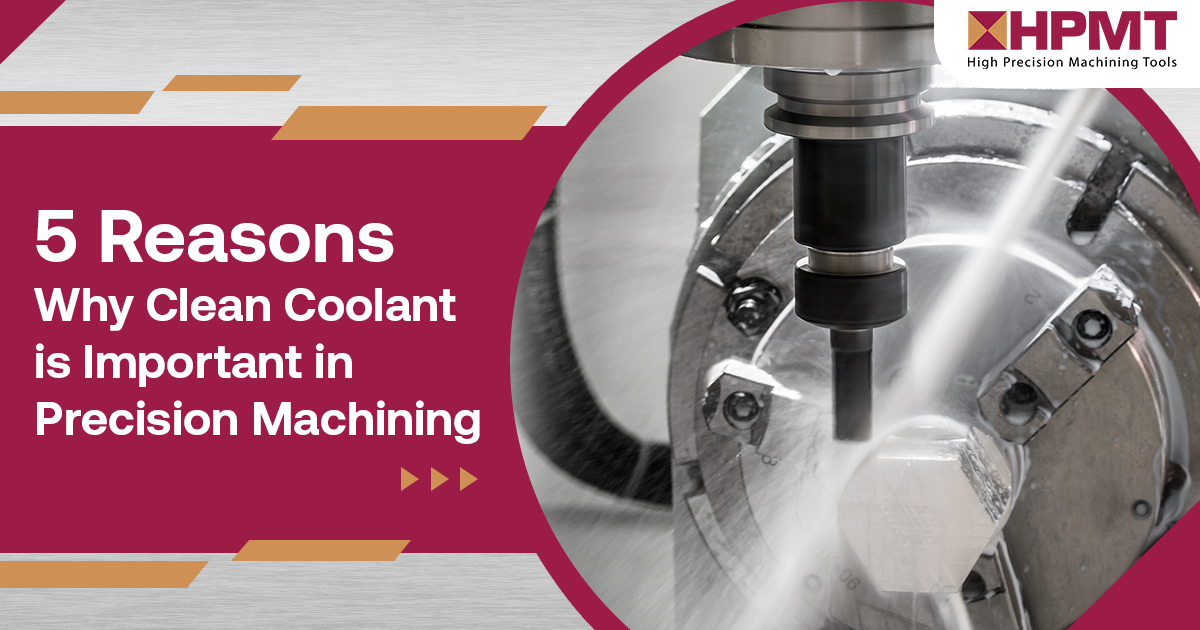
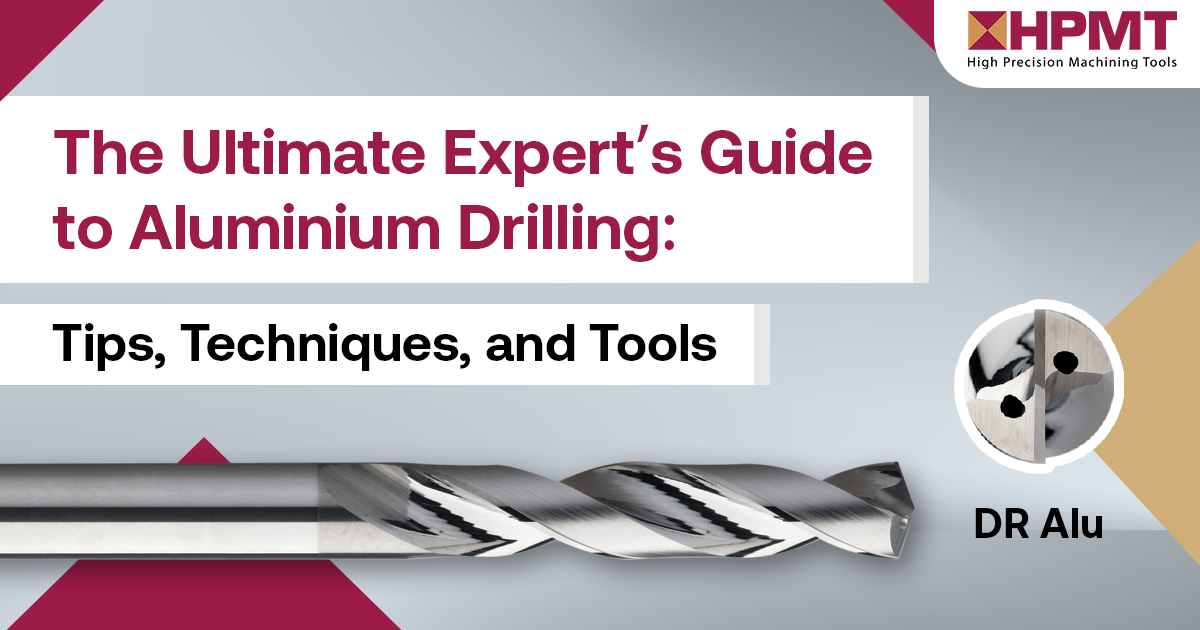
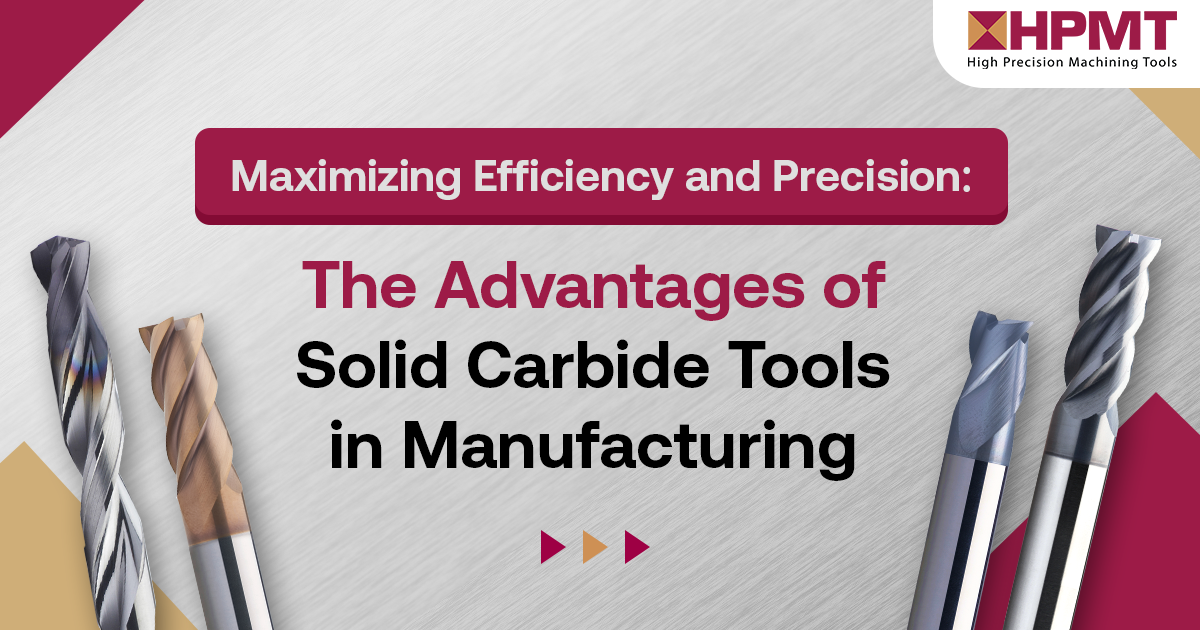